In today’s fast-paced world of manufacturing and logistics, it is crucial to have efficient and reliable systems in place to protect your valuable products. One such system that has become increasingly popular is the stretch wrapper, also known as a pallet wrapping machine or pallet wrapper. This innovative tool provides a secure and uniform layer of stretch wrap around palletized loads, ensuring stability and protection during transit or storage.
Gone are the days of manually wrapping pallets with layers of plastic film, only to find inconsistencies in tension and coverage. With a stretch wrapper, you can automate the entire process, significantly boosting efficiency and reducing the risk of product damage. Whether you are in the food and beverage industry, retail, or manufacturing, mastering the stretch wrapper is guaranteed to streamline your operations and provide peace of mind.
The stretch wrapper, often referred to simply as a stretch wrap machine, works by rotating the pallet while a roll of stretch film is unwound automatically. As the pallet spins, the film is stretched and applied tightly, creating a secure bond that protects the contents from shifting, moisture, dust, and other potential hazards. Additionally, some stretch wrappers offer adjustable settings, allowing you to customize the number of revolutions and the tension applied, further enhancing the stability and integrity of your palletized loads.
Importance of Proper Pallet Wrapping
Proper pallet wrapping is essential for businesses that rely on efficient and secure transportation of their products. A pallet wrapping machine, also known as a pallet wrapper or stretch wrap machine, plays a key role in ensuring that goods are well-protected and ready for shipment. In this section, we will explore the importance of proper pallet wrapping in boosting efficiency and protecting your products.
First and foremost, a correctly wrapped pallet provides stability during transit. By securely wrapping the load, you minimize the risk of items shifting or toppling over. This is especially crucial when products are stacked or there are fragile items involved. Without proper wrapping, you run the risk of damage to your products, resulting in potential losses for your business.
Stretch Wrapping
Furthermore, proper pallet wrapping helps to safeguard your products from various external factors. This includes protection against dust, dirt, moisture, and UV rays. By creating a protective barrier, the stretch wrap acts as a shield, preventing any contaminants from compromising the quality of your goods. This is particularly important for products that are sensitive to environmental conditions or need to adhere to strict quality standards.
In addition to protecting your products, proper pallet wrapping also enhances the efficiency of your operations. A pallet wrapping machine enables you to wrap your pallets quickly and consistently, reducing the time and effort required compared to manual wrapping. This is especially beneficial for businesses dealing with high volumes of shipments, as it allows for faster preparation and loading of goods onto trucks or storage areas.
In conclusion, the importance of proper pallet wrapping cannot be overstated. By investing in a reliable pallet wrapping machine and ensuring that your products are securely wrapped, you can boost efficiency within your supply chain and protect your goods from potential damage. Take the necessary steps to master the use of a stretch wrapper, and you will reap the rewards of smoother operations and satisfied customers.
Choosing the Right Stretch Wrapper
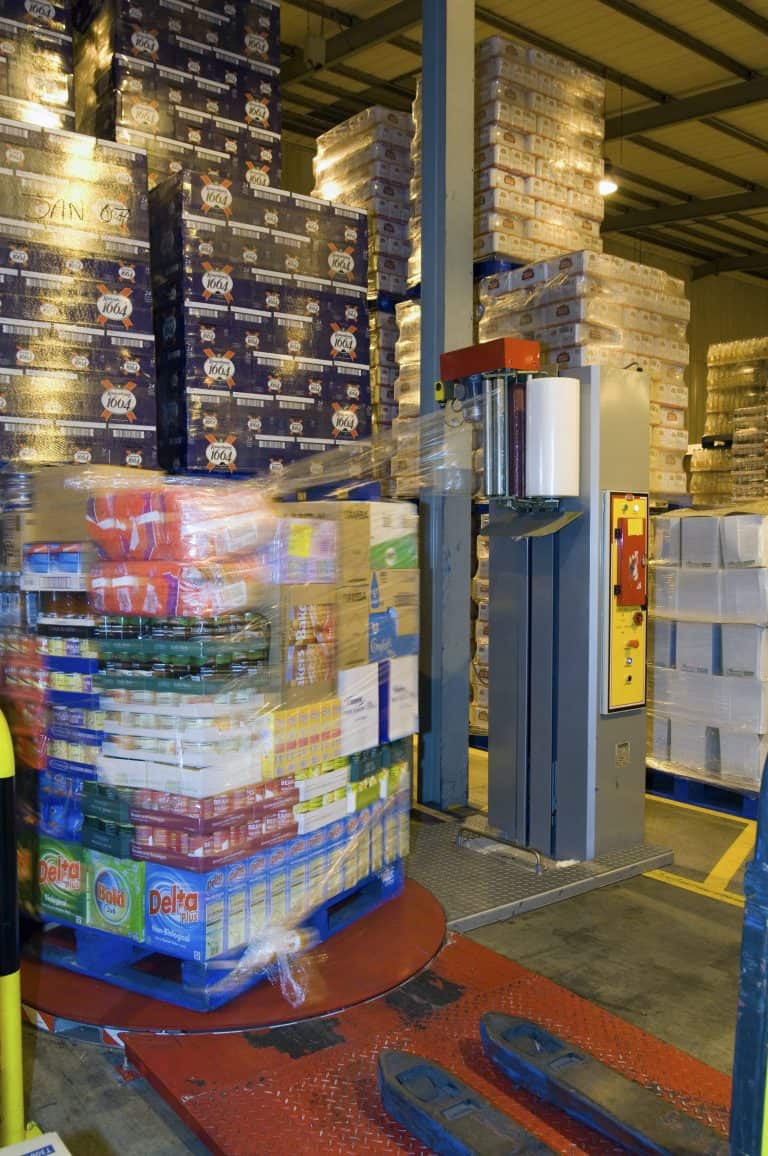
When it comes to selecting the perfect stretch wrapper for your needs, there are a few key factors to consider. Understanding these factors will help you make an informed decision and ensure that you choose the right pallet wrapping machine for your specific requirements.
Size and Capacity: The first thing to consider is the size and capacity of the stretch wrapper. You need to determine the dimensions and weight of the pallets that will be wrapped. This information will help you choose a pallet wrapper that can handle your specific load size and weight. It is important to select a stretch wrap machine that can effectively wrap your pallets without any issues.
Automation Level: The level of automation required is another crucial factor to consider. Different businesses have different needs and requirements, so it is important to choose a stretch wrapper that aligns with your automation goals. If you have a high volume of pallet wrapping needs, an automated stretch wrapper may be the best choice. However, if your pallet wrapping needs are relatively low, a semi-automatic or manual stretch wrapper may be more suitable.
Film Type and Compatibility: The type of stretch film you plan to use and its compatibility with the stretch wrapper is another important consideration. Ensure that the stretch wrapper you select is compatible with the type and width of stretch film you intend to use. This will guarantee efficient wrapping and optimal product protection.
By considering these factors – size and capacity, automation level, and film type and compatibility – you can choose the right stretch wrapper that will boost efficiency and effectively protect your products during transit and storage.
Mastering the Stretch Wrapping Technique
To truly master the stretch wrapping technique, it is important to understand the key principles behind operating a pallet wrapping machine effectively. By following these guidelines, you can boost efficiency and ensure maximum protection for your products.
Adjusting the Tension: One of the most crucial aspects of mastering the stretch wrapper is finding the right tension for the stretch wrap. Too much tension can cause damage to the products, while insufficient tension can result in loose wraps that fail to secure the load effectively. Experiment with different tension settings to find the optimal balance for your specific products and their packaging requirements.
Proper Load Placement: Another important aspect of mastering the stretch wrapper is properly placing the load on the turntable. Ensure that the load is centered and aligned correctly to avoid any imbalances that could lead to wrapping issues or load instability. Take the time to neatly arrange the products on the pallet to maximize stability and minimize the chance of movement during the wrapping process.
Optimizing Wrap Patterns: Different products and load types may require specific wrap patterns for optimal security and stabilization. By understanding the various wrap patterns available on your pallet wrapper, you can choose the most suitable one based on the shape, size, and weight of your load. Experiment with different patterns, such as spiral or cross patterns, to find the one that provides the best results for your specific packaging needs.
By mastering the stretch wrapping technique and implementing these guidelines, you can increase efficiency, minimize product damage, and ensure the safe transportation of your goods. Remember to regularly maintain and inspect your pallet wrapper to keep it in optimal condition, and provide adequate training to operators to guarantee proper usage of the machine. With these practices in place, your stretch wrapping process can become a streamlined and reliable part of your product packaging workflow.